Ситроен джампи микроавтобус где собирают
Содержание статьи:
Фото Отзывы владельцев Citroen Jumper (Ситроен Джампер) с ФОТО Видео Похожие статьи
Комфортный модульный салон. Вместительность до 8 человек. Узнайте подробнее!
Калужский завод «ПСМА Рус» запустил полный цикл производства среднеразмерных фургонов Peugeot Expert и Citroen Jumpy. Россия стала второй страной, где Группа PSA наладила выпуск этих легких коммерческих автомобилей.
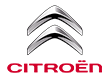
Citroen Jumper представляет собой одно из наиболее обширных семейств в линейке продуктов французского бренда. Машина успешно справляется с перевозкой грузов и пассажиров. Данная модель – это не просто средство передвижения, а современный и комфортный автомобиль. Дизайн и конструкция Ситроен Джампер практически полностью совпадают с оформлением и устройством Фиат Дукато и Пежо Боксер. Объясняется это тем, что разработчиками моделей является совместное предприятие данных брендов (Sevel Sud). На российском рынке Citroen Jumper не является лидером своего сегмента, уступая в популярности моделям Пе.
Без гиперссылки или в печати - см. Интересно, что первоначально он был местом для хр Рассылка Лучшие материалы Авторевю — в вашем почтовом ящике Предоставляя e-mail, вы подтверждаете свое согласие с условиями политики конфиденциальности. Чтобы автомобили были доступны более широкой массе клиентов, Группа PSA совместно с PSA Bank подготовила специальное лизинговое предложение, действующее на всей территории России. В зависимости от модификации, здесь может быть по одной, или по две рессоры.
Как собирают Peugeot Expert и Citroen Jumpy в Калуге
Фокус на сегмент легкого коммерческого транспорта обусловлен более оптимистичной ситуацией в этой части авторынка. Cборка новых фургонов дополняет производство текущих моделей Группы PSA: Все автомобили будут собираться на одной линии.
Сборка в режиме CKD предусматривает сварку кузова из штамповок, поставляемых из Франции. Производство, рассчитанное на выпуск тыс. По соседству с линией седанов, где собирают все французские автомобили, располагается производство кроссоверов Mitsubishi Outlander и нового Pajero Sport.

Всего на заводе работают человек. В процессе подготовки производства новых моделей коммерческих фургонов существующая сборочная линия подверглась модернизации. В частности, были расширены габариты постов на конвейере российские версии фургонов на 10 см выше и на 60 см длиннее европейских , а логистика перестроена так, чтобы обеспечить всю необходимую номенклатуру комплектующих для более гибкого процесса номенклатура деталей выросла в два раза.
Также были соответствующим образом адаптировано все настроечное и испытательное оборудование. Важно, что все эти трансформации были реализованы калужской командой без привлечения зарубежных специалистов. Полный цикл изготовления автомобиля длится около 40 часов. А начинается все на линии формирования кузова, где на специальных стендах-кондукторах собирают воедино элементы силовой структуры, пол, колесные арки, моторный отсек.

Затем в нижней части кузова монтируются резьбовые шпильки. Сварочные работы выполняются как в ручном, так и в автоматическом режиме, всего насчитывается около сварных точек. Далее свое место занимают боковины, а после приварки крыши кузов в металле приобретает законченную форму, на нем появляется российский VIN. А несколько готовых изделий, выбранных в течение смены в случайном порядке, отправляются на координатно-измерительный комплекс, где проверяется не только геометрия, но и качество сварных точек, включая прочностные характеристики.
На заводе в основном используется европейское и корейское оборудование. В Калуге об этом упоминают не без гордости. Покраска фургона длится в общей сложности примерно 9 часов. За это время на кузов наносится 6 килограммов лака, краски, мастик и антикоррозионных материалов. Разумеется, используются экологически чистые акриловые эмали на водной основе. В главный сборочный цех кузова поступают на подвесном конвейере.
Седаны и фургоны компонуются группами по 12 единиц. Гибкое производство позволяет перестроить конвейер от модели к модели без остановок. Сборка начинается с укладки шумоизоляции, жгутов электропроводки и монтажа приборной панели. Затем при помощи манипулятора вклеивается ветровое стекло, собираются элементы внутренней отделки. Далее окончательная сборка подкапотного пространства, укладка резиновых прокладок и уплотнительных соединений, установка колес.
В частности, локализованы такие детали, как бампер и пластиковые элементы обвеса передка, шины и колесные диски, панель приборов, сиденья, отделка кабины, включая пластиковые элементы, коврики и все стекла. На будущее стоит задача удвоить количество компонентов, производимых в России. Решается вопрос о местном производстве силовых установок, по примеру Volkswagen и Mercedes-Benz. Длина сборочной линии К0 превышает 1 км, всего на ней порядка 90 постов.
По мере перемещения от поста к посту автомобиль заправляется маслами, техническими жидкостями, топливом и реагентом AdBlue. Попутно проверяется герметичность тормозной системы. Перед входом в световой тоннель выполняется финальная регулировка зазоров дверей, капота и багажника. Далее полный аудит внешнего вида готового автомобиля, регулировка фар, запуск двигателя. Оживший фургон отправляется своим ходом сначала на стенд схода-развала, затем в тропический душ и на испытательный трек, где, помимо прочего, замеряется внутренний шум.